Our company can offer air handling units with
the following types of heat recovery :
ROTARY HEAT RECYCLER

The rotary recycler consists of alternating flat and corrugated plates made of aluminum foil. This arrangement creates a large number of smooth channels through which air flows in laminar mode. This provides a low pressure drop and reduces the risk of dust and dirt deposits in the ducts. The rotor rotates with an electric motor. At low outside air temperatures, moisture can be returned from the exhaust air. Therefore, with strict requirements for moisture transfer, it is necessary to use a hygroscopic rotor. The rotor can also be used to utilize cooling energy. In this case, it is also advisable to use a hygroscopic rotor.
The efficiency of heat recovery can reach 80...85% depending on the quantitative and qualitative characteristics of the supply and exhaust air.
The flow of air between the flows of supply and exhaust air does not exceed 2...3 %.
Optionally, the rotary recycler can be equipped with a speed regulator.
CROSS HEAT RECYCLER

The cross recycler consists of aluminum plates. The plates form insulated channels through which the supply and exhaust air in the cross direction exchange heat energy through the aluminum walls. Special assembly technology makes the heat exchanger airtight, which avoids overflow between supply and exhaust air.
At low supply air temperatures, moisture will condense from the exhaust air with additional heat release. The cross recycler section is equipped with a stainless steel tray for collecting and draining condensate. Optionally, the section can be equipped with a hydraulic siphon.
When condensing, there is a risk of the recycler freezing. Freezing can be avoided by passing part of the supply air through the bypass line. All cross recyclers sections are equipped with a bypass channel with an air valve to control the direction of air flow.
The efficiency of heat utilization is up to 70% depending on the quantitative and qualitative characteristics of the supply and exhaust air.
The airtightness of the channels is 99.9% at a pressure of 500 PA.
The maximum pressure difference between supply and exhaust air should not exceed 1500 Pa.
COUNTERWEIGHT HIGH EFFICIENCY RECYCLER
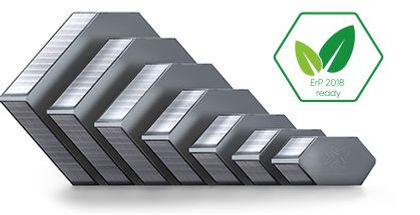
In units a highly efficient countercurrent plate recuperator is used . A corrosion-resistant alloy aluminum alloy is used as the material for the plates. The flows of fresh air and exhaust air are completely separated and directed counterclockwise along thin parallel aluminum plates. Transfer of moisture and odors from one stream to another is excluded.
At low supply air temperatures, moisture will condense from the exhaust air with additional heat release. The counter-current recycler module is equipped with a stainless steel drainage tray.
Condensation can cause the recycler to freeze. To prevent this, the unit is equipped with a bypass with an air valve and actuator.
GLYCOL HEAT RECYCLER
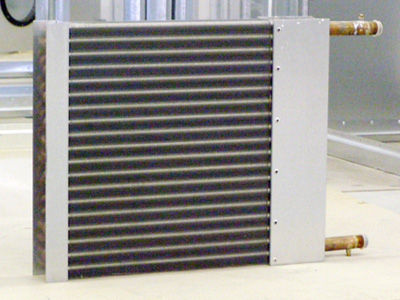
The glycol recycler consists of two sections of heat exchangers: one is located in the supply part, and the second - in the exhaust. This disposal system is very convenient when the supply and exhaust parts of air handling units are spaced apart at some distance. Heat transfer occurs through the circulation of the glycol mixture (usually a concentration of 40..45%) between two heat exchangers.
The supply and exhaust parts of the unit can be at a significant distance from each other. This distance is regulated only by the characteristics of the circulation pump (not included).
The section of the heat exchanger in the exhaust part is additionally equipped with a drainage tray made of stainless steel and a drip trap. Optionally can also be equipped with a hydraulic siphon.
The efficiency of heat utilization is up to 45..50% depending on the quantitative and qualitative characteristics of the supply and exhaust air.
The maximum glycol content can be up to 50%.